Liquid Compounds
We produce high-quality liquid compounds for vibratory and centrifugal finishing. These formulations are designed to deliver excellent cleaning, polishing, and deburring results, trusted across industries for their performance and reliability.
Liquid compounds
Liquid compounds in vibratory finishing are like their liquid counterparts to powdered ones. They offer similar benefits but in a water-based solution:
- All-in-one action: Just like powdered compounds, they can cut down on steps by deburring, smoothing, cleaning, and sometimes lubricating parts during the vibratory finishing process.
- Cleaning power: They often contain detergents and cleaners to remove oils, greases, and contaminants effectively.
- Media protection: Some liquid compounds can extend the lifespan of the finishing media by preventing them from getting clogged with metal fines or debris.
- Safety: Controlled dosing reduces H&S risks and offers automatic operation with no operator input
- Foam control: Unlike some powdered compounds that can cause excessive foaming, liquid varieties are formulated to minimise foaming, ensuring the vibratory machine functions efficiently.
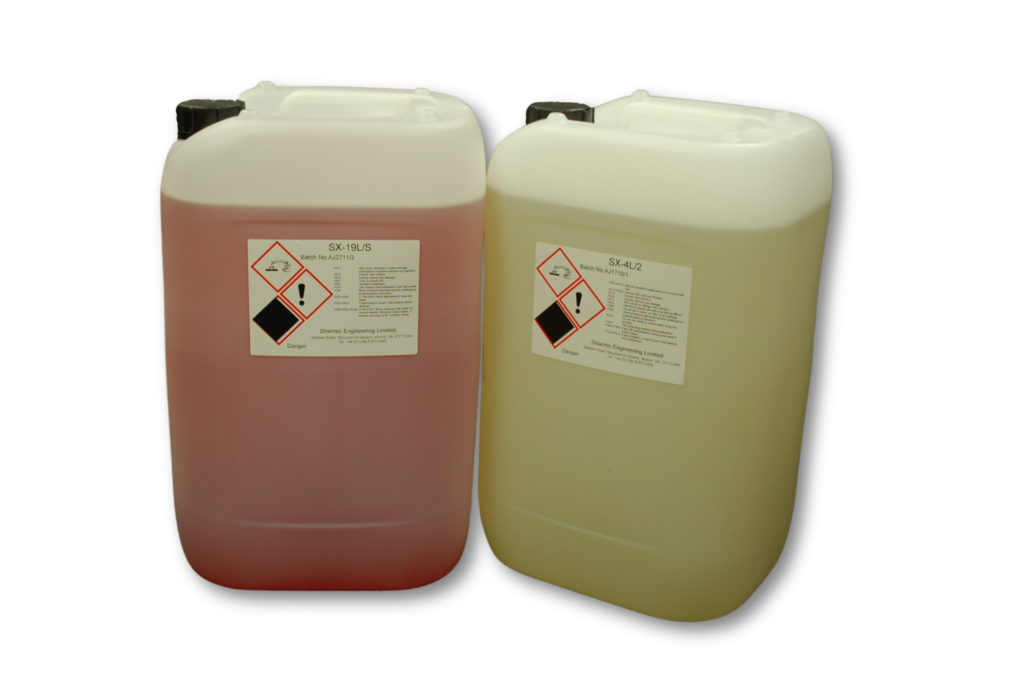
SKU | Materials | Function | Ferrous | Non-Ferrous | Deburr | Descale | Degrease | Polish | Burnish | Protection | Smoothing | Neutralise |
---|---|---|---|---|---|---|---|---|---|---|---|---|
ALP37 | Universal | Ultrasonic Clean | ✔ | ✔ | ✔ | |||||||
SX-1L/Xi/2 | Universal | General Purpose | ✔ | ✔ | ✔ | ✔ | ✔ | ✔ | ||||
SX-3L | Bright Surfaces W/Steel Media | Burnishing | ✔ | ✔ | ✔ | |||||||
SX-4L/2 | Aluminium/Brass/Zinc | Cleaning/Polishing | ✔ | ✔ | ✔ | ✔ | ✔ | |||||
SX-5L | Steel | Cleaning/Polishing | ✔ | ✔ | ✔ | ✔ | ✔ | ✔ | ||||
NORCHEM 80 | Copper/Brass/Alum/S Steel | Polishing | ✔ | ✔ | ✔ | ✔ | ||||||
NORCHEM 89 | Aluminium/Zinc | Cleaning/Polishing | ✔ | ✔ | ✔ | ✔ | ||||||
NORCHEM 150 | Cast Iron/Steel | Cleaning/Polishing | ✔ | ✔ | ✔ | ✔ | ✔ | ✔ | ✔ | |||
NORCHEM HILITE | Pewter/Silver/Gold/Plastic/Rubber | Polishing | ✔ | ✔ | ✔ | ✔ | ||||||
SX-9L | Stainless Steel | Polishing | ✔ | ✔ | ✔ | |||||||
SX-10L | Brass/Copper/Steel/Aluminium | Acidic Cleaning/Polish | ✔ | ✔ | ✔ | ✔ | ✔ | ✔ | ✔ | ✔ | ||
SX-12L | Reduces Excess Foam | Antifoam | ✔ | ✔ | ||||||||
SX-16L | Tin/Pewter/Silver | Polishing | ✔ | ✔ | ✔ | ✔ | ✔ | ✔ | ||||
SX-19L/S | Steel/Stainless Steel | H/D Degrease | ✔ | ✔ | ✔ | ✔ | ✔ | ✔ | ||||
SX-20L | Brass/Copper/Aluminium | Polishing | ✔ | ✔ | ✔ | ✔ | ||||||
SX-22L | Steel | Dewatering Oil | ✔ | ✔ | ||||||||
SX-25L | Steel/Non-Ferrous | Degreasing | ✔ | ✔ | ✔ | ✔ | ✔ | |||||
SX-90L | Steel/Stainless Steel/Aluminium | Polishing | ✔ | ✔ | ✔ | ✔ | ✔ | |||||
RPP2 | Steel | Inhibitor | ✔ | ✔ | ✔ | |||||||
RP19L/S | Steel | Degrease/Inhibitor | ✔ | ✔ | ✔ | ✔ | ✔ |
Why choose our finishing compounds?
Manufactured in house in Worcestershire, UK
We have complete control over the quality of our compounds, from formulation to production.
Constantly monitored for performance
We use our own demonstration facilities and subcontract finishing department to test the performance of our compounds in real-world conditions.
Specifically formulated for a variety of functions
Our compounds are designed to meet the specific needs of your metal finishing process.
Formulated for different application methods
Our compounds can be used with manual or automated dosing systems and in open or closed systems.
Contain additives to isolate metal fines
Clean the machine work chamber, and protect processed components and metallic machine parts: Our compounds help to ensure a clean and efficient finishing process.
Committed to developing more environmentally friendly compounds
We work closely with our collaborators to research and develop new compounds that are less harmful to the environment.