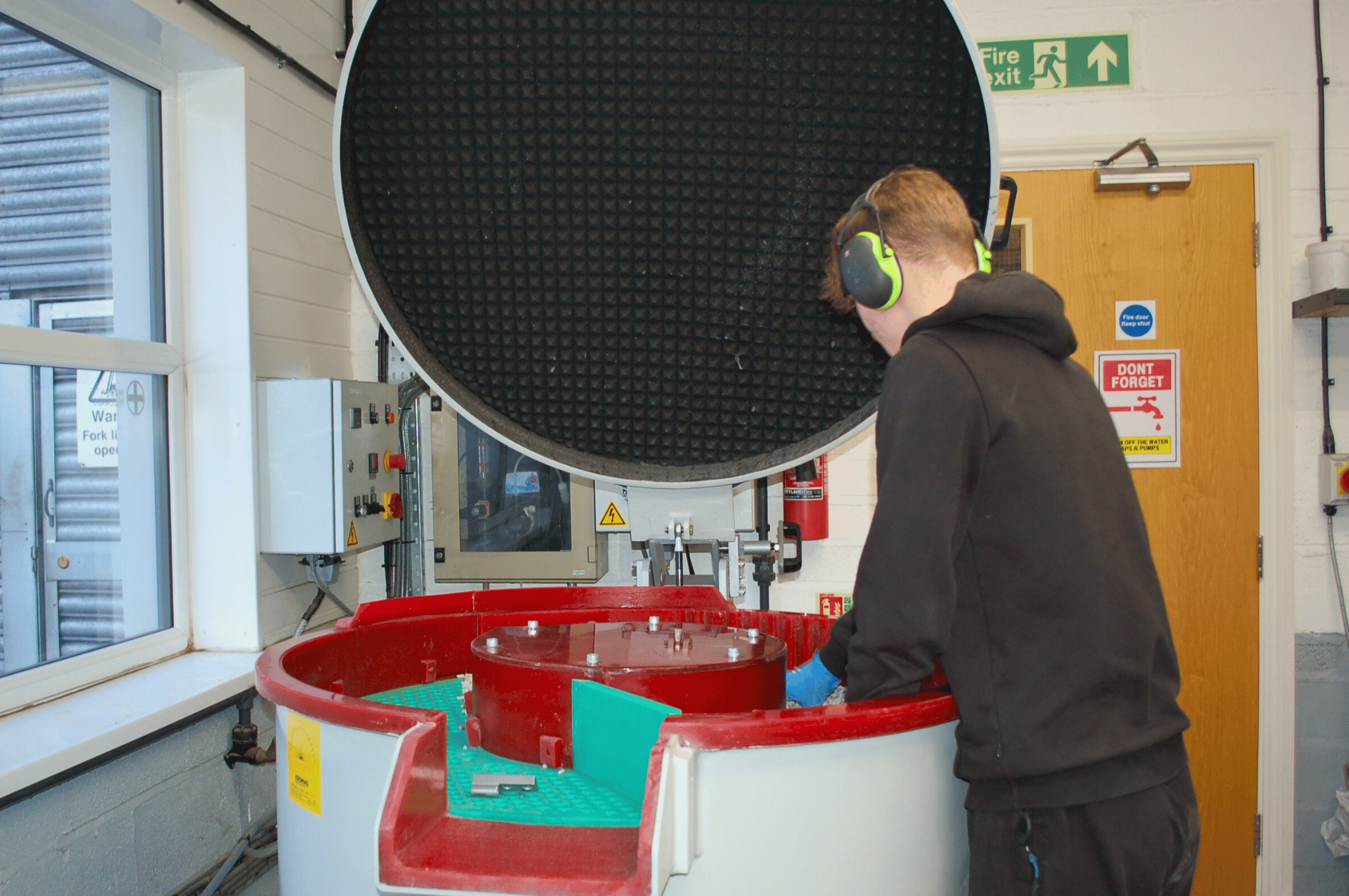
Professional Finishing Services Tailored to You
Our subcontract division offers professional vibratory surface finishing services tailored to your needs. We provide expert finishing for various components using advanced machinery and skilled technicians. Partnering with us ensures high-quality results without the need for equipment investment, allowing you to focus on your core business while we handle your finishing requirements efficiently.

Polishing involves improving the surface finish by removing microscopic imperfections and imparting a smooth, mirror-like appearance. Vibratory polishing uses fine abrasive media, compounds along with vibration to achieve a high level of surface smoothness and lustre.
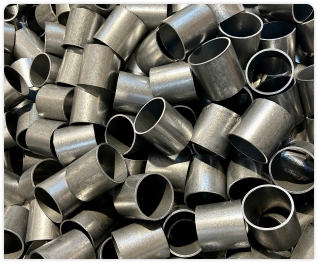
Deburring is a crucial step in surface finishing, as it removes sharp edges, burrs, and other unwanted protrusions that can hinder functionality and cause safety hazards. Vibratory deburring employs a combination of mechanical action, abrasive media, and vibratory energy to effectively remove these imperfections.
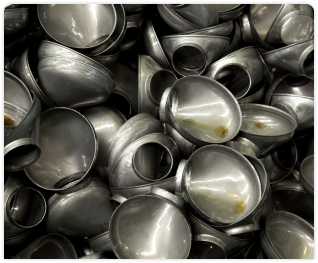
Degreasing is essential for preparing surfaces for subsequent finishing processes and ensuring product cleanliness. Vibratory degreasing employs solvents or detergents in combination with vibration to effectively remove oil, grease, and other contaminants from metal and plastic components.
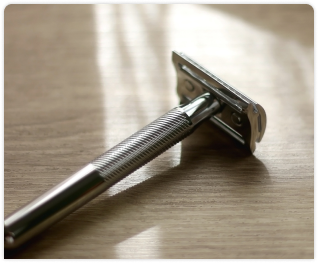
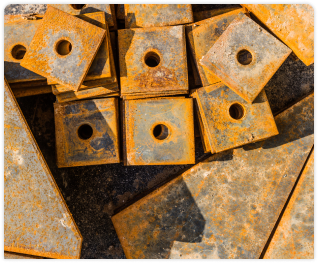
Surface protection is essential for extending the lifespan and performance of manufactured components. Vibratory processes can incorporate various protective coatings, to enhance corrosion resistance, wear resistance, and aesthetic appeal.

Smoothing involves refining the surface texture of a component, reducing overall roughness, and removing any coarse or uneven areas. Vibratory smoothing uses abrasive media and compounds to achieve a smoother, more uniform surface finish.
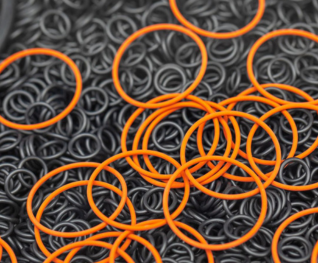
Deflashing is the process of removing unwanted thin ridges or protrusions (flash) that form on plastic parts during the moulding process. Flash typically appears along the parting line, which is the meeting point of the two halves of the mould.

Descaling involves removing unwanted deposits like rust, scale, and oxides from metal surfaces. Vibratory descaling uses abrasive media, such as ceramic, beads or shot, to mechanically abrade the surface, removing these impurities and revealing the underlying clean metal.

Unlock specialised knowledge and expertise!
Our team of skilled technicians possesses extensive experience in vibratory finishing, enabling us to tackle complex finishes and challenging materials. We are well-equipped to manage both high-volume and specialised orders, ensuring your specific requirements are met.
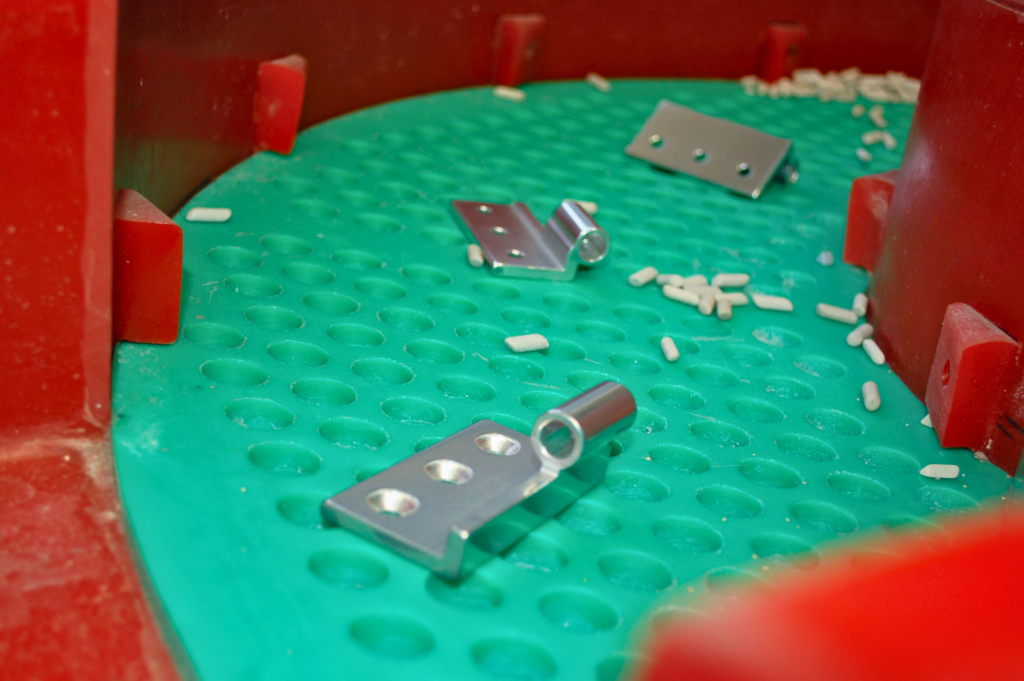
Streamline your operations with subcontracting
Whether you lack the resources, expertise, or production volume to maintain your own finishing facility, our subcontracting service offers a compelling alternative. We manage the entire finishing process, from initial consultation to the final finished product, ensuring consistent quality and efficiency.

Seamless transportation for worry-free service
Our team can manage the entire transportation process, from picking up your components to delivering the finished products, ensuring a seamless and hassle-free experience. We adhere to strict safety protocols and timeliness commitments.